Occupational health and safety
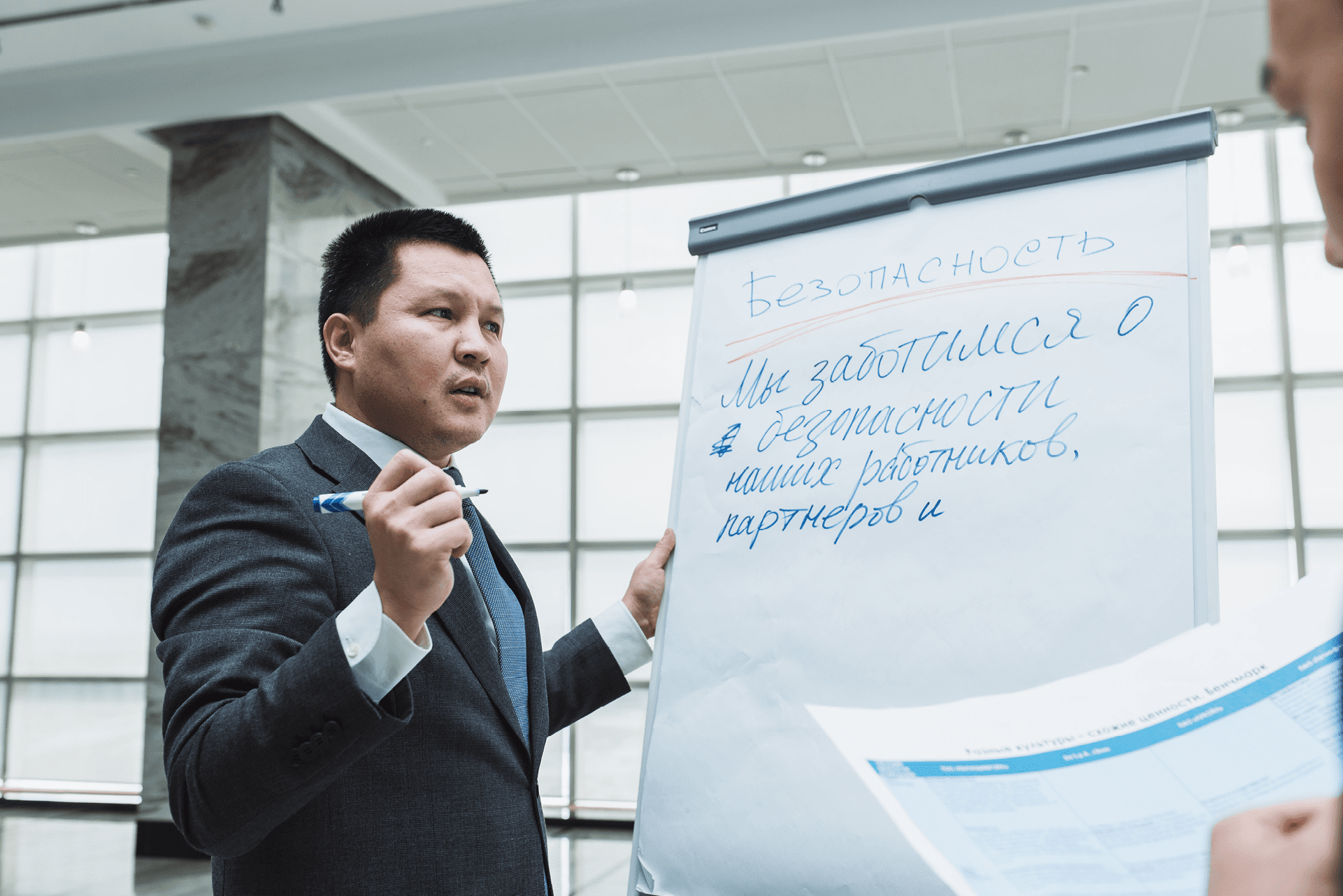
KMG’s Occupational Health and Safety Policy is driven by our senior management setting the tone at the top in occupational health and safety and engaging every employee in building a robust safety culture. Management teams at KMG and its subsidiaries and associates take a zero tolerance approach to losses and damage caused by accidents (including traffic accidents), emergencies, as well as by the use of alcohol, narcotic drugs, psychotropic substances or their analogues. KMG is committed to ensuring compliance with both national laws and relevant international and national standards.
Key highlights Occupational health and safety | Unit | 2019 | 2020 | Change | % |
---|---|---|---|---|---|
Accidents | Acc. | 41 | 30 | –11 | –27 |
Number of injuries | People | 48 | 32 | –16 | –33 |
Road accidents | Acc. | 44 | 15 | –29 | –66 |
Fires | Acc. | 6 | 6 | –4 | –40 |
Indicator | 2016 | 2017 | 2018 | 2019 | 2020 | |
---|---|---|---|---|---|---|
Lost Time Incident Rate (LTIR), per 1 mln person-hours | 0.49 | 0.42 | 0.32 | 0.31 | 0.22 | 0.24 |
Fatal Accident Rate (FAR), per 100 mln person-hours | 4.5 | 3.25 | 0.65 | 1.28 | 0.0 | 0.46 |
2020 highlights
The health and safety of our employees are a top priority for KMG, and we remain committed to our zero injuries vision, i.e. achieving 100% safety. We have made significant progress on health and safety over the past five years. Our employees are engaged on safer working conditions and adoption of the highest standards to better protect themselves, their colleagues, and others. But there is still room for improvement.
In 2020, no work-related fatalities were reported for the first time in KMG’s history. Furthermore, since KMG joined the International Association of Oil & Gas Producers (IOGP) in 2018, its road accident and injury rates were below IOGP benchmarks.
In 2020, the number of work-related accidents decreased by 27% year-on-year (from 41 accidents in 2019 to 30 in 2020), with the number of injuries down by 33% (from 48 in 2019 to 32 in 2020).
The number of road accidents dropped by 66% (from 44 in 2019 to 15 in 2020), and the number of fires fell by 40% (from 10 in 2019 to 6 in 2020).
Process safety management
In 2020, KMG set out to improve process safety, aiming to prevent major accidents with disastrous consequences (manmade accidents, incidents and disasters) within the Company. For this purpose, the Company approved a new standard for process safety management at KMG’s facilities. The standard establishes uniform requirements for, and effective approaches to, asset and process equipment integrity maintenance, safe operating rules, norms, and procedures as per the requirements of Kazakh laws and best international practices (IOGP, OSHA), as well as process risk identification and prevention/mitigation.
Digitisation of HSE processes
- The Trip Management project was initiated to improve transport safety, foster a safe driving culture and establish a single centralised digital platform. Currently, the project is being piloted at JSC Embamunaigas.
The project aims to improve road safety through instilling a safe driving culture based on global best practice, advanced digital solutions, and process automation. The project will also unify the trip safety management requirements for all ground transport operations, implement a centralised tracking of key metrics and enable improved fleet utilisation through analytical reports and corporate-level indicators.
The Trip Management project’s next steps:
- connect vehicles leased by JSC Embamunaigas to a single monitoring system by the end of 2021
- roll out the project solutions to other subsidiaries and associates.
- Development of environmental monitoring methodology project was commenced to enhance our environmental performance. The project aims to improve transparency, enable rapid responses, and minimise errors in environmental records, analysis, monitoring and management across KMG Group. A demo version of the information system was presented based on a pilot successfully run at a production company. The full roll-out and commercial launch of the automated environmental monitoring information system across KMG Group is scheduled for 2021.
HSE KMG information system upgrade
The HSE KMG system consists of the following modules:
- Reporting – generation of HSE reporting forms
- Observation – behavioural observations of work practices and driving safety
- Actions – internal inspection planning and activity supervision
- Protection – identification and alerts on unsafe condition/behaviour/action/hazardous event/factor, as well as improvement of occupational health and safety system
- HSE Condition Analysis – surveying and collecting proposals from KMG Group employees
- Records and Investigation – recording all types of incidents; incident investigations
- Internal Control and Monitoring – audits by multidisciplinary teams, detection of irregularities
- Analytics – automated HSE analysis and visualisation of consolidated data. Plans are in place to roll out the HSE KMG system across the entire KMG Group during 2021
Workplace culture improvement and HSE promotion activities
- An analysis of well servicing and workover incidents was followed up by the development of an Action Plan to improve well servicing and workover trip safety.
- 68 booklets and leaflets on HSE and prevention of injuries, accidents and coronavirus infection are circulated weekly across subsidiaries and associates and the Corporate Centre, with ongoing interaction and advice for specialists at subsidiaries and associates
- Videos on the following subjects have been produced and disseminated:
- Lessons learned from well servicing and workover trip incidents
- Lessons learned from road accidents
- System rolled out at KMG to manage emergencies and crises and respond to all types of incidents (manmade accidents, fires, cyber-attacks, supply disruptions, financial crises, etc.)
- Workplace exercise
- Subsidiaries and associates have been audited for compliance with HSE requirements, including preparedness for the second wave of the coronavirus infection, with follow-up recommendations on improvement.
- In order to evaluate, analyse, and mitigate HSE risks of KMG Group’s contractors, quarterly reports on contractors’ HSE breaches, including summary of penalties imposed, are submitted to KMG’s Board of Directors.
- In order to reduce the risk of fires and damage to employees’ health and property, an inspection of subsidiaries and associates was conducted, covering fire-protection, heating and power-supply systems as well as compliance with rules and procedures for process equipment operation in accordance with fire safety rules and internal regulations with due consideration of production process specifics.
- Contractors were also inspected, with follow-up recommendations. Fire safety documentation package (schedules, plans, Inspection Report, fire fighting plan, manuals, etc.) have been developed. Fire drills involving personnel and responding fire vehicles were conducted on sites in accordance with the applicable schedules.
A number of preventive technical measures were taken:
- Maintenance and repair of automated security and fire detection, firefighting and fire alarm systems to ensure the operability of equipment through periodic preventive maintenance, condition monitoring and correction of typical malfunctions specified in operating documentation and maintenance procedures
- Fire safety inspections
- Inspection of first-aid fire fighting equipment, water supply equipment, etc.
Fires and significant HSE incidents are promptly reported to KMG’s Board of Directors as per the instruction on prompt alerts to the Board issued at a Board meeting.
Upon completion of investigation, relevant materials, including an investigation report specifying immediate and root causes and financial damage, copies of orders on disciplinary actions against employees guilty of the incident, as well as documents specifying post-investigation changes, and documents aimed at preventing similar incidents in the future, are submitted to KMG’s Board of Directors.
Occupational health and hygiene
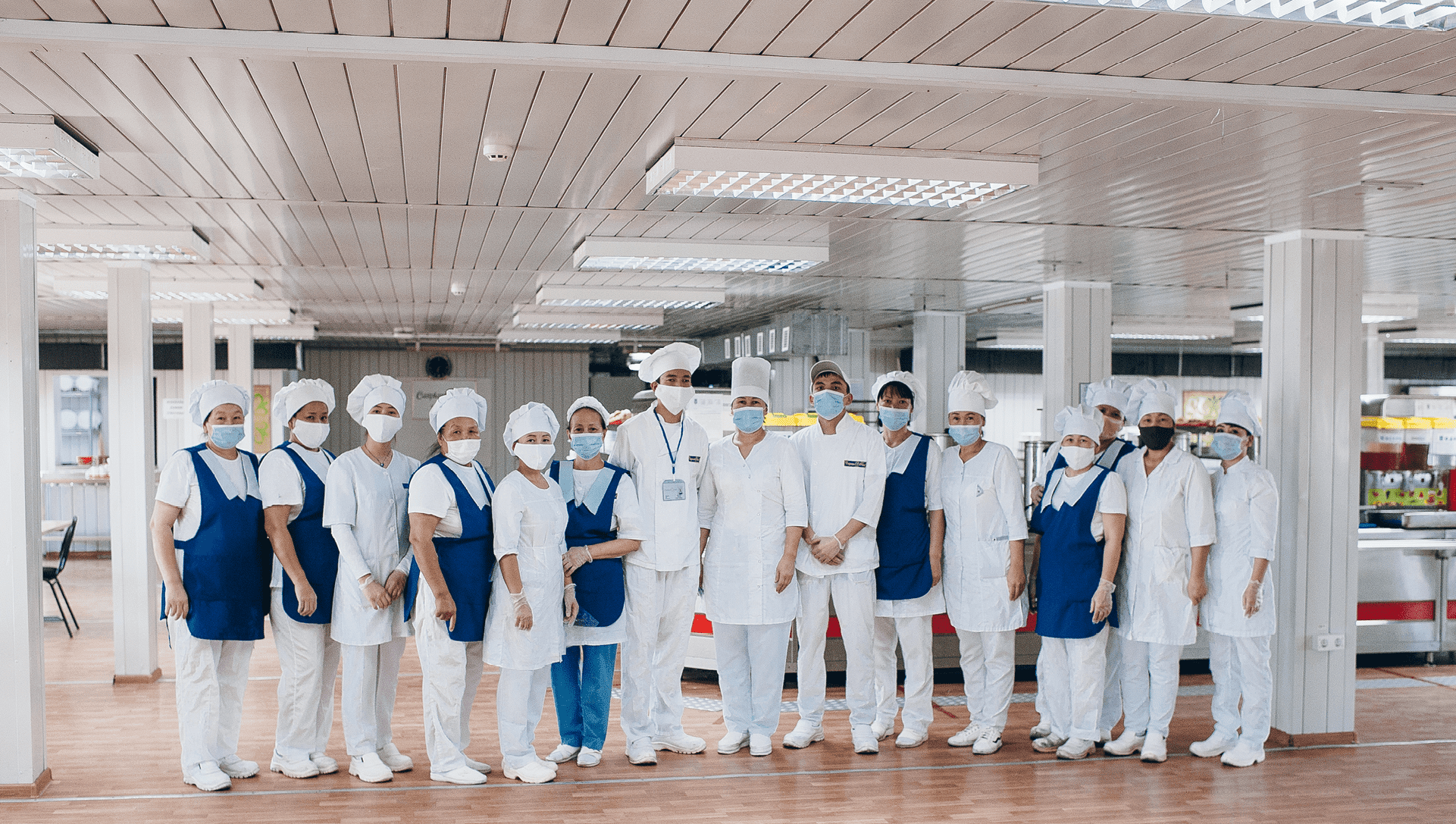
The Company manages occupational health and hygiene matters in accordance with the requirements of Kazakh laws and international occupational health standards. KMG is strongly focused on employee health protection and improvement, irrespective of the specific production process involved.
In 2020, employees of subsidiaries and associates lost 287,075 work days to illness, up 124,922 days, or 43%, year-on-year. The number of non-injury related fatalities among employees of subsidiaries and associates reduced by five incidents, or 38%, year-on-year.
To ensure better and more effective management within the Company, an occupational health and hygiene management system is in place, offering tools to assess compliance with requirements for the provision of materials and equipment to corporate primary care facilities, risk management, medical emergency response arrangements and overall occupational health and hygiene management.
Main goals of the Company’s occupational health and hygiene management system:
- Setting uniform requirements for process set-up to maintain and improve employees’ health
- Identifying and mitigating risks (work-related hazards) by improving occupational hygiene, ergonomics and workplace hygiene
- Monitoring and taking preventive measures based on the assessment of employees’ health risks to mitigate the risks
- Promoting and encouraging a healthy lifestyle during and outside of working hours.
The Company’s occupational health and hygiene management system implementation is evaluated twice a year (every six months), followed by the development of improvement initiatives.
The Company regularly implements a range of measures to improve working conditions and prevent occupational diseases across its operations.
KMG continued its Heart Attack and Stroke Prevention campaign aimed at the prevention and reduction of employee fatalities related to cardiovascular diseases. The Company also tracks and monitors the implementation of the 10 Steps to Better Health initiative and the corporate standard for emergency medical response, setting uniform requirements for employee access to emergency treatment procedures, medical centre equipment and the emergency medical response action plans.
In 2020, 55 employees of KMG’s Corporate Centre were trained in first aid.
A draft of the Employee Health Management Framework and 2021–2023 Implementation Roadmap for its phased roll-out were developed in order to improve health services provided to KMG employees (healthcare services and health insurance).
- A working group established
- First Aid protocol booklet prepared
- A video on workplace exercise released
- Letters on the coronavirus infection prevention and preparedness to respond to worsening epidemiological situation sent out to subsidiaries and associates
- Joint presentations with Mediker on the coronavirus infection prevention for the KMG Corporate Centre employees
- Weekly circulation of booklets, leaflets and videos on the coronavirus infection prevention to the Corporate Centre and subsidiaries and associates; ongoing interaction and advice for specialists of subsidiaries and associates
- Interaction with the Committee for Quality Control and Safety of Goods and Services under the Ministry of Healthcare of the Republic of Kazakhstan
- Organisation and coordination of PCR testing for the KMG Corporate Centre employees
- Subsidiaries and associates audited to check the preparedness for the second wave of the coronavirus infection (Mangistaumunaigaz, KazTransOil (Mangistau Oil Pipeline Management Department), service companies: Oil Services Company, Oil Transport Corporation, and Oil Construction Company), with follow-up recommendations.
Progress and ongoing initiatives on preventing the spread of COVID-19
At the beginning of the pandemic, the Company took early action to prevent the spread of COVID-19.
As the situation worsened during the first wave of the coronavirus infection, most cases were registered in the western regions.
This was attributable to the fact that most employees were concentrated on sites operating on a fly-in fly-out (FIFO) basis and were required to take PCR tests before and after fly-in periods (resulting in a higher detection rate compared to hydrocarbon refining and processing companies where employees work in shifts and crews).
The highest incidence and fatality rates were registered in early July, as the national state of emergency was lifted (on 11 May 2020).
With the onset of the pandemic, in order to reduce the incidence rate and curb the spread of COVID-19 as well as to mitigate its impact on production processes, we implemented a range of comprehensive measures, drafted and adopted guidelines and policies, and developed and approved specific action plans:
- The coronavirus infection pandemic response protocol
- On measures to prevent the introduction and spread of COVID-19
- On phased relaxation of lockdown restrictions and preparation for a potential new wave of the coronavirus infection
- Ensuring worker and employee safety and health
- On improving corporate accountability and implementing timely and effective measures to prevent and mitigate mass outbreaks of the viral disease among employees and at operations in the worst-case scenario, including the introduction of strict lockdown measures
The Company has implemented and maintains measures across the three phases of response to prevent the spread of the coronavirus infection:
Phase 1 – pre-lockdown measures
Phase 2 – lockdown measures kept in place
Phase 3 – tighter restrictions when disease outbreaks are identified
To support the action plan implementation, response protocols were activated for coronavirus infection detection and spread, providing for a range of sanitary and epidemiological control measures, including:
- Introduction of lockdown measures
- Mass testing of employees
- Workforce reduction at operating facilities
- Suspension of non-critical activities (well drilling, completion, servicing, workover)
- Business travel restrictions, ban on mass gatherings and shift to remote management
- Longer fly-in periods for staff working on the FIFO basis (from 7 to 14 days and from 14 to 28 days)
- Demobilisation of non-essential personnel from operating facilities and projects; workforce reduction at oil and gas fields to keep operations running with a skeleton staff.
Currently, the range of preventive measures and strict disinfection and sanitary protocols are still in place across KMG Group’s operations. All employees, including those working from home, were instructed to ensure strict compliance with sanitary, hygiene and anti-epidemic rules. Also, instructions and leaflets are circulated on a regular basis.
Administrative staff was shifted to work from home as far as possible (50% to 100%). Non-essential personnel within the risk group that can not take leave or be shifted to remote work (staff that keeps operations running) is idled.
All FIFO personnel and contractors are tested for the coronavirus infection before fly-in.
Back-up crews have been formed, which are not involved in operations and do not contact other personnel. The back-up personnel are used in operations only when primary operational staff gets infected and quarantined.
Fly-in personnel accessing the sites (or personnel returning to their workplaces after working remotely or from leaves) are briefed on the coronavirus infection prevention and pandemic precautions (hygiene protocols, use of sanitiser and masks, social distancing) as well as other occupational safety rules.
Also, to prevent the coronavirus infection and comply with anti-epidemic rules, regular awareness raising activities are ongoing, with posters and recommendations on prevention, disinfection. sanitation and hygiene protocols circulated.
Social distancing, mandatory mask-wearing rules, use of hand sanitiser, pre-shift health screenings, temperature taking before, during, and after work are all in place across KMG and its subsidiaries.
Protocols to be followed if infection is suspected or detected have been developed and implemented. All employees have been advised of the need to promptly report test results and their first symptoms of the coronavirus infection upon discovery as well as of the liability for withholding such facts, test falsification, or quarantine breach.
Remote camps and other designated locations provide space for quarantining self-isolating asymptomatic carriers of the coronavirus infection.
Materials, goods, works and services necessary for the protection of people and disinfection of spaces are procured in an accelerated process.
Emergency response teams at subsidiaries monitor the situation and the spread of the coronavirus infection. The teams stay in touch with local executive authorities and authorised governmental agencies at all times.
The crisis management team of KMG’s Corporate Centre stays abreast of how the situation evolves, with a 24/7 monitoring procedure in place. The heads of the operation-level emergency response teams report periodically or as necessary on the situation, its impact on operations and measures taken to prevent the spread of the coronavirus infection among their respective workforce. These meetings result in decisions and recommendations on preventing the spread of the coronavirus infection.
KMG Group also provided over KZT 6.2 bln worth of assistance to local governments and healthcare facilities. Specifically, we purchased medical equipment (ventilators) and related materials, ambulances, personal protective equipment, and provided support in rolling out additional beds.
With the measures taken, the situation is currently stable, and we adjust business continuity plans and reprioritise business processes and contractual obligations to other parties depending on the epidemiological situation.
Measures to prevent contracting the coronavirus and curb its spread are still in place, including the following:
- Previously introduced protocols (adjusted to incorporate lessons from the first wave) to curb the coronavirus spread and maintain anti-epidemic measures, stricter sanitation and disinfection protocols and other sanitary rules
- Critical business processes were identified, along with emergency recovery options for the processes, as well as essential personnel, suppliers, materials, and equipment
- Business continuity and critical business process recovery plans were developed
- Efforts to ensure the preparedness of first-aid facilities are ongoing with due preparations for a potential increase in laboratory examinations and coronavirus infection vaccination
- Stocks of PPE (medical masks, respirators, gloves), dispensers, sanitiser, and disinfecting solutions we built up, along with life-support kits to protect life and health
- Longer fly-in periods are still in place with greater focus on advising employees of the need for self-monitoring of symptoms, good hygiene and compliance with safety rules (staying alert and safe), and social distancing
- Arrangements were made for an accelerated procurement process and uninterrupted supply of goods, works and services in case of worsening epidemiological situation
- Continuous monitoring procedures are in place to curb the spread of the coronavirus infection, and cooperation was established between public and contracted health services to support the implementation of preventive and lockdown measures as well as to facilitate joint responses in the event of worsening epidemiological situation.
To facilitate these measures, a number of initiatives were implemented jointly with contracted health services, including:
- Adding competent medical practitioners
- Maintaining a minimum stock of essential medical equipment, medicines and PPE
- Procurement of necessary medical equipment
- Adding staff to first-aid facilities and call centres to provide information and remote advice
- Improved access to scheduled healthcare services for employees with non-infectious diseases
- Developing joint plans to protect employees’ life and health through COVID-19 response measures.
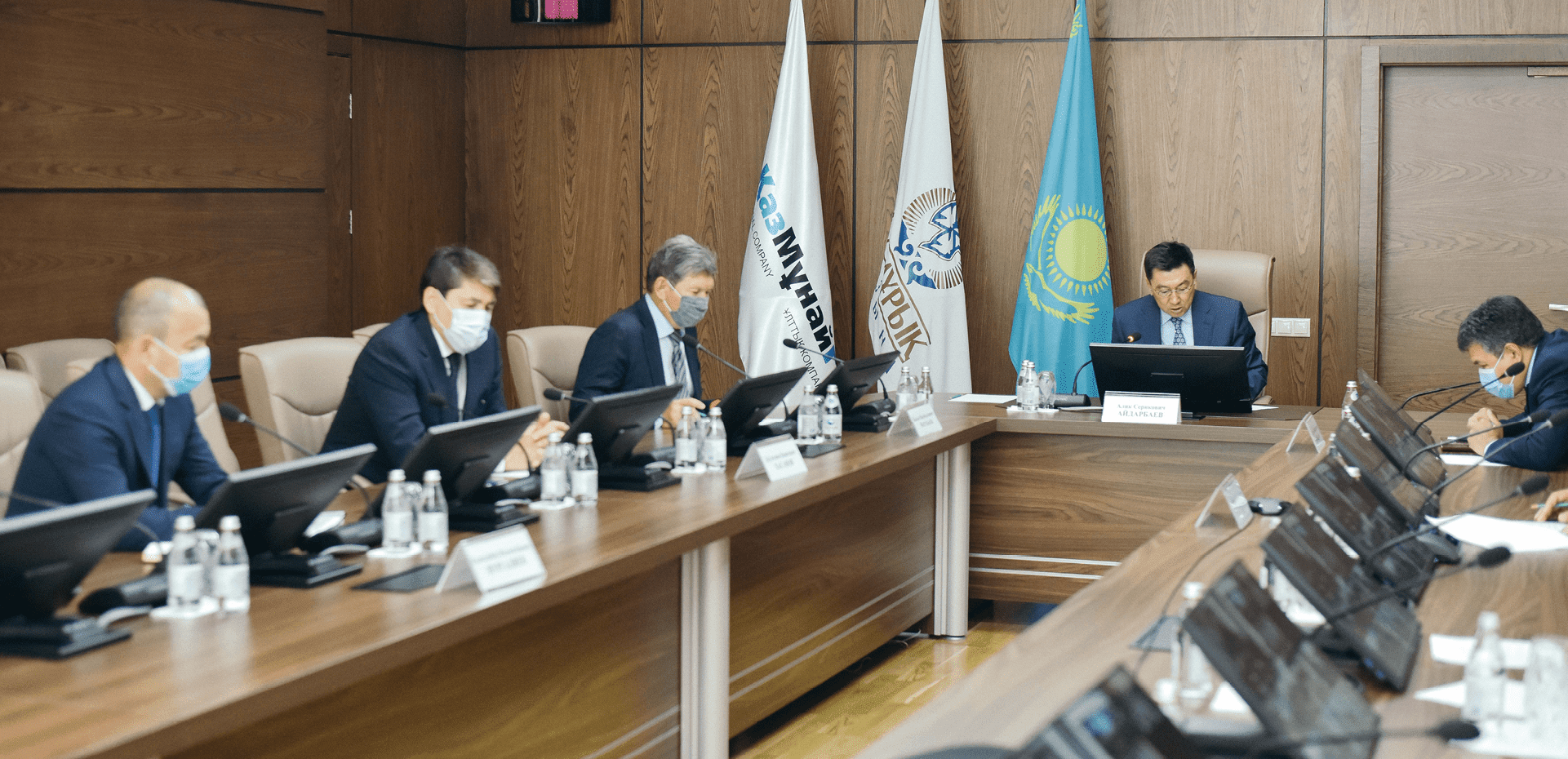